- Member ID
- #2049
- Messages
- 98
- Reactions
- 321
- Likes
- 27
- City
- Frederick
- State
- CO
- Country
- United States
- Vehicle
- Challenger Hellcat
[TL;DR - We are now developing an Inconel625/718 based rotor]
(Fun Fact: One of the DOT standards for brakes is to test a car at BOTH 90% Vmax and Gross vehicle weight - Who does this?)
==============================================
(A couple of on-car shots of two different iterations)
=================================
=================================
It has been some time since we've spoken to the public on the open forum, and excuses being what they are, we've had issues to contend with.
We've been testing various iterations of core design, coatings (more on this in a bit) and slight variations in material, both on the brake-dyno in Detroit as well as on-car testing with @BULL's Challenger. And while there was a certain level of success in that testing, our goal is not to deliver anything short of 100%. If we weren't trying to satisfy halo-car drivers, for cars that weigh 4400lbs and can achieve 200mph, we might have been done ages ago.
(Fun Fact: One of the DOT standards for brakes is to test a car at BOTH 90% Vmax and Gross vehicle weight - Who does this?)
==============================================
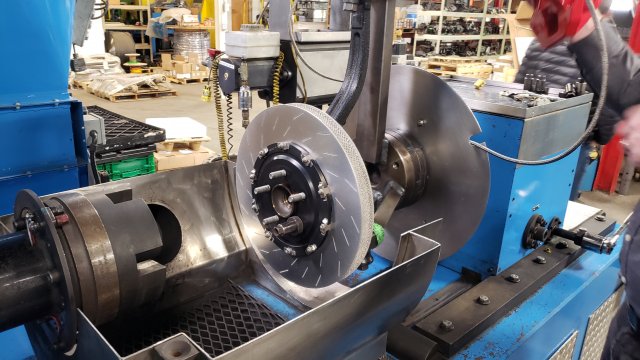
(A couple of on-car shots of two different iterations)
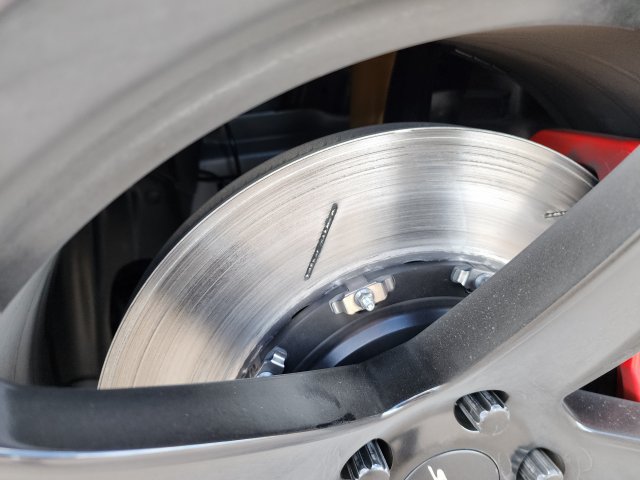
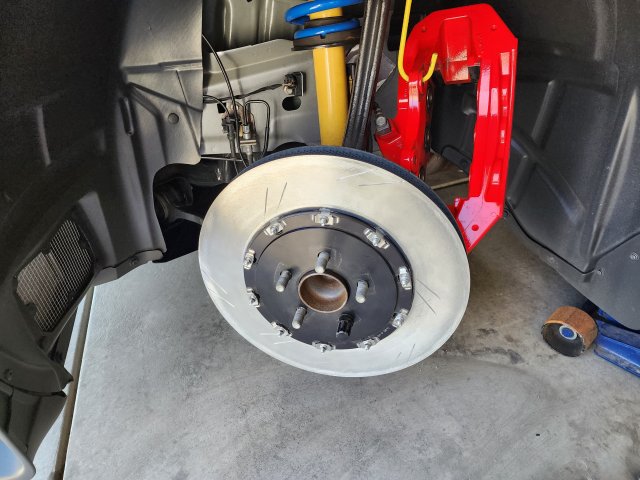
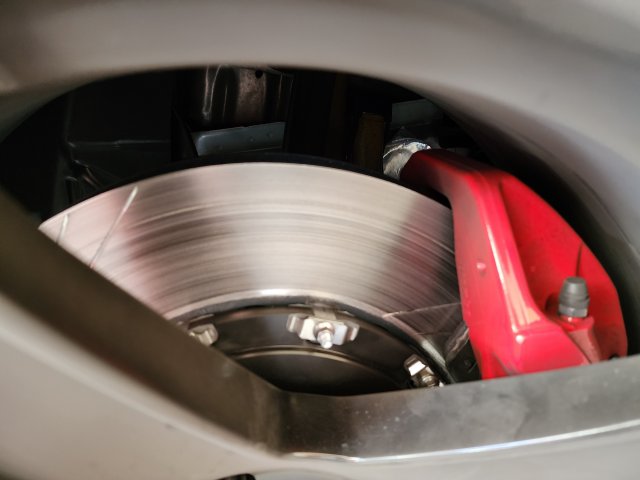
=================================
Ultimately, our original A1000-RAM10 material, was not fully compatible with "off the shelf" pad linings. We were working with a few different pad manufacturers, but ultimately our focus was on the rotor and being able to provide a solution to the broader market, not one that required a specific and "only" pad material.
Earlier, "coatings" were mentioned. One of these coatings was a nickel based "cold-spray" application, and this was very promising, but had adhesion issues. As a result, it was scrapped from development, but we never forgot the initial performance realized in this design iteration. Pad CoF (Coefficient of Friction) was very good!
- Our primary goal was, and is, to offer a rotor at least as light as carbon-fiber, for notably less money, longer life than cast-iron, more durable than other exotic offerings, and at least the same performance, not only for drag racing (light weight/E.T.), but also road racing (CoF/Heat). Not an easy task.
=================================
3D printing is at the heart of this design challenge, it allows for a heat-exchanger design (really what a brake rotor is) that can not be cast due to internal channels and paths, as well as what is generally referred to as "thin-wall" features. In a simplified way, these features are the basis for our patent. This is what makes this rotor so much better, it's ability to dissipate heat energy. All materials have various thermal properties, and among other reasons, this is why we initially chose the A1000-RAM series material. The thermal conductivity is very high. The initial A1000 designs that went to Detroit to be tested, on the same brake-dynos that the Big-Three use, performed so well that the technicians had to dramatically shorten the dwell time between test sections because the rotor was cooling off so much faster than they were used to!
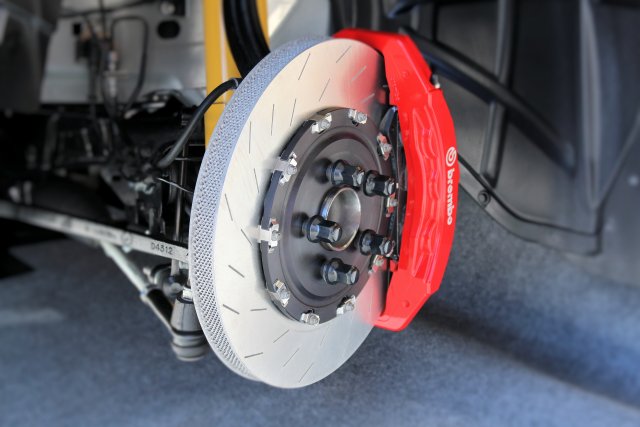
But in the end, we need to move on to another material that is more inline with the industry and the OTS pad linings that we all love and use. Remember that nickel cold-spray coating? Here comes Inconel...
Inconel is an advanced aerospace "super-alloy" and is normally reserved for the toughest design jobs like holding jet engines together. It has very good high-temperature performance and is not only very strong, but also very corrosion resistant due to it's high nickel content. It is also one of the leading materials that is being used in advanced 3D metal printing. By contrast it is heavy compared to the A1000 that we were using, however it makes up for it in high-temperature strength, so we can use much thinner wall sections in our "core". Another benefit to this is that in heat-exchanger design, a thin-wall feature is able to shed energy at a proportionally faster rate than the same material in a "thick-wall" condition, despite having the same thermal coefficient! We did gain a bit of mass, but don't worry, they're still lighter than the CF offerings and it is fully expected that the pad compatibility issues that we've been fighting should be addressed! We don't like to share CAD images because we think they tend to be less than fully credible, but as soon as we have some good shots available, we'll post them up.
The very first Inconel units recently came off of the printer and are headed to post-processing. It won't be long now before they are in testing, and while we don't plan on shortcutting testing, it's expected that because this material is at its heart a "steel", and not an aluminum-ceramic MMC, things should progress with less "issues".
Feel free to ask questions and discuss, we'll answer what we can...
-
15
-
9
-
2
- Show All